In the current business environment, where competition is fierce, control over supply chain expenses has become critical for organizations looking to stay profitable and continue expanding. Every stage of the supply chain, from sourcing to distribution, offers chances to reduce costs and boost efficiency.
This article explores some of the best tactics used by business executives to negotiate the tricky landscape of supply chain expenses.
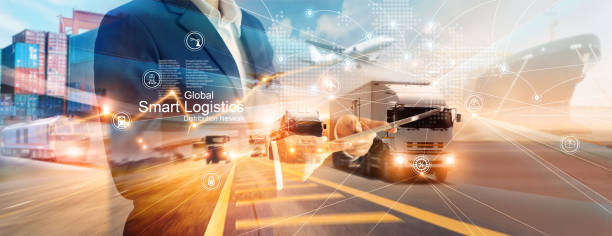
A complex strategy that takes into account several factors, including technology integration, inventory control, transportation logistics, and supplier relationships, is required for cost management in the supply chain. Organizations can identify inefficiencies and implement targeted solutions to drive cost reduction without sacrificing quality or customer satisfaction by utilizing data analytics and innovative practices.
With the help of professional opinions and real-world examples, we examine the essential strategies used by prosperous companies to optimize their supply chains and save long-term costs.
Businesses are always changing their tactics to stay ahead in the fast-paced market of today, whether it’s by investing in cutting-edge tracking technology, negotiating advantageous supplier contracts, or putting just-in-time inventory systems into place.
Come along on a journey through the complexities of supply chain cost management as we unearth best practices and actionable insights to support companies in thriving in an era of never-before-seen opportunities and challenges.
How Do You Manage Supply Chain Costs?
A comprehensive strategy that takes into account all facets of the supply chain process is needed to manage supply chain costs. Here are a few crucial tactics:
- Supplier Relationship Management (SRM): Cultivating strong relationships with suppliers is crucial for negotiating favourable terms, including pricing, payment terms, and delivery schedules. By collaborating closely with suppliers, companies can identify opportunities for cost savings, such as bulk-purchasing discounts or long-term contracts.
- Demand Planning and Forecasting: Accurate demand forecasting helps companies optimize inventory levels and minimize excess inventory costs. By using historical data, market trends, and predictive analytics, businesses can anticipate demand fluctuations and adjust their production and procurement accordingly, reducing the risk of stockouts or overstock situations.
- Inventory Management: Implementing efficient inventory management practices, such as just-in-time (JIT) inventory systems or vendor-managed inventory (VMI) programs, can minimize carrying costs and reduce the risk of obsolescence. By maintaining optimal inventory levels, companies can free up working capital and improve cash flow while ensuring product availability.
- Transportation Optimization: Optimizing transportation routes and modes can significantly reduce shipping costs and improve delivery efficiency. Leveraging technology solutions, such as route optimization software or transportation management systems (TMS), allows companies to consolidate shipments, minimize empty miles, and negotiate better freight rates with carriers.
- Warehousing Efficiency: Streamlining warehouse operations can lower storage costs and enhance order fulfilment speed. By implementing warehouse management systems (WMS) and lean principles, companies can improve inventory accuracy, reduce handling times, and maximize space utilization, ultimately driving down operational expenses.
- Process Automation: Automating manual processes and workflows can increase productivity and reduce labour costs throughout the supply chain. Whether it’s automating order processing, inventory replenishment, or invoice reconciliation, investing in technology solutions such as robotic process automation (RPA) or enterprise resource planning (ERP) systems can yield significant cost savings over time.
- Continuous Improvement: Adopting a culture of continuous improvement enables companies to identify and address inefficiencies proactively. By regularly reviewing supply chain processes, soliciting feedback from stakeholders, and benchmarking against industry best practices, organizations can identify areas for optimization and implement corrective actions to drive ongoing cost reduction and performance improvement.
To summarize, an integrated strategy that incorporates various aspects such as demand planning, warehouse management, transportation efficiency, inventory optimisation, process automation, and ongoing improvement projects is necessary to effectively manage supply chain expenses.
In today’s fast-paced business world, companies can become more competitive and cost-efficient by implementing these strategies and utilizing technology solutions.
What Are Handling Costs In Supply Chain Management?
The expenses incurred during the handling and movement of goods throughout the various stages of the supply chain are referred to as handling costs in supply chain management. These expenses may cover a broad range of tasks and procedures related to the actual handling, storing, and delivery of goods from suppliers to final consumers. Handling expenses may consist of:
- Material Handling: Costs associated with the physical handling of raw materials, components, and finished goods within manufacturing facilities, warehouses, and distribution centres. This includes activities such as loading and unloading trucks, palletizing, sorting, and picking orders.
- Storage and Warehousing: Costs related to storing inventory in warehouses or storage facilities, including rent or lease expenses, utilities, insurance, and property taxes. Warehousing costs also include labour costs for receiving, put-away, inventory management, order picking, packing, and shipping.
- Transportation: Costs associated with transporting goods between different locations in the supply chain, including inbound transportation from suppliers, outbound transportation to customers, and inter-facility transfers. Transportation costs can include fuel, vehicle maintenance, driver wages, insurance, tolls, and shipping fees charged by carriers.
- Packaging: Costs related to packaging materials, such as boxes, pallets, shrink wrap, and cushioning materials, as well as the labour and equipment required for packaging and labelling products for shipment. Efficient packaging practices can help minimize handling costs by reducing the risk of damage during transit and optimizing space utilization.
- Order Processing: Costs associated with processing customer orders, including order entry, order verification, order picking, packing, and order fulfilment. Streamlining order processing workflows and implementing automation technologies can help reduce handling costs by improving efficiency and accuracy.
- Returns and Reverse Logistics: Costs associated with handling product returns and managing reverse logistics processes, including inspecting returned goods, restocking inventory, processing refunds or exchanges, and disposing of or refurbishing returned items. Efficient reverse logistics practices can help minimize handling costs and recover value from returned products.
- Inventory Carrying Costs: While not directly related to physical handling, inventory carrying costs can also impact overall supply chain handling costs. These costs include expenses such as financing costs, storage costs, obsolescence costs, and opportunity costs associated with holding inventory in the supply chain.
The physical transportation, warehousing, and processing of goods along the supply chain are all included in the broad category of activities and costs associated with handling costs in supply chain management. These expenses can be reduced, and overall supply chain profitability and efficiency can be raised, by streamlining handling procedures and utilizing technological solutions.
Conclusion
The costs incurred during the actual transportation, warehousing, and processing of goods along the supply chain are referred to as handling costs in supply chain management. These expenses cover a wide range of tasks like order processing, inventory carrying, material handling, warehousing, transportation, packaging, and returns management.
Reducing operating costs, increasing overall profitability, and optimizing supply chain efficiency all depend on efficient handling cost management. Businesses can accomplish this by putting strategies into place like better inventory management procedures, automating processes, utilizing automation technologies, and optimizing warehouse layouts.
Organizations may obtain a competitive advantage in the market by concentrating on lowering handling costs while preserving or raising service standards. Further, opportunities for cost reduction and operational improvement must be found through ongoing monitoring, analysis, and handling process optimization.
Essentially, a comprehensive strategy that unifies people, procedures, and technology throughout the supply chain is needed to minimize handling costs. Businesses may achieve long-term success and sustainable cost savings in the fast-paced business world of today by placing a high priority on accuracy, efficiency, and customer satisfaction.